The Chemistry Behind ZAM®'s Excellent Performance
Research
Our parent company, NIPPON STEEL, completed 12 years of research and development before producing the first ton of zinc-aluminum-magnesium alloy coated steel sheet (ZAM®) in 2000.
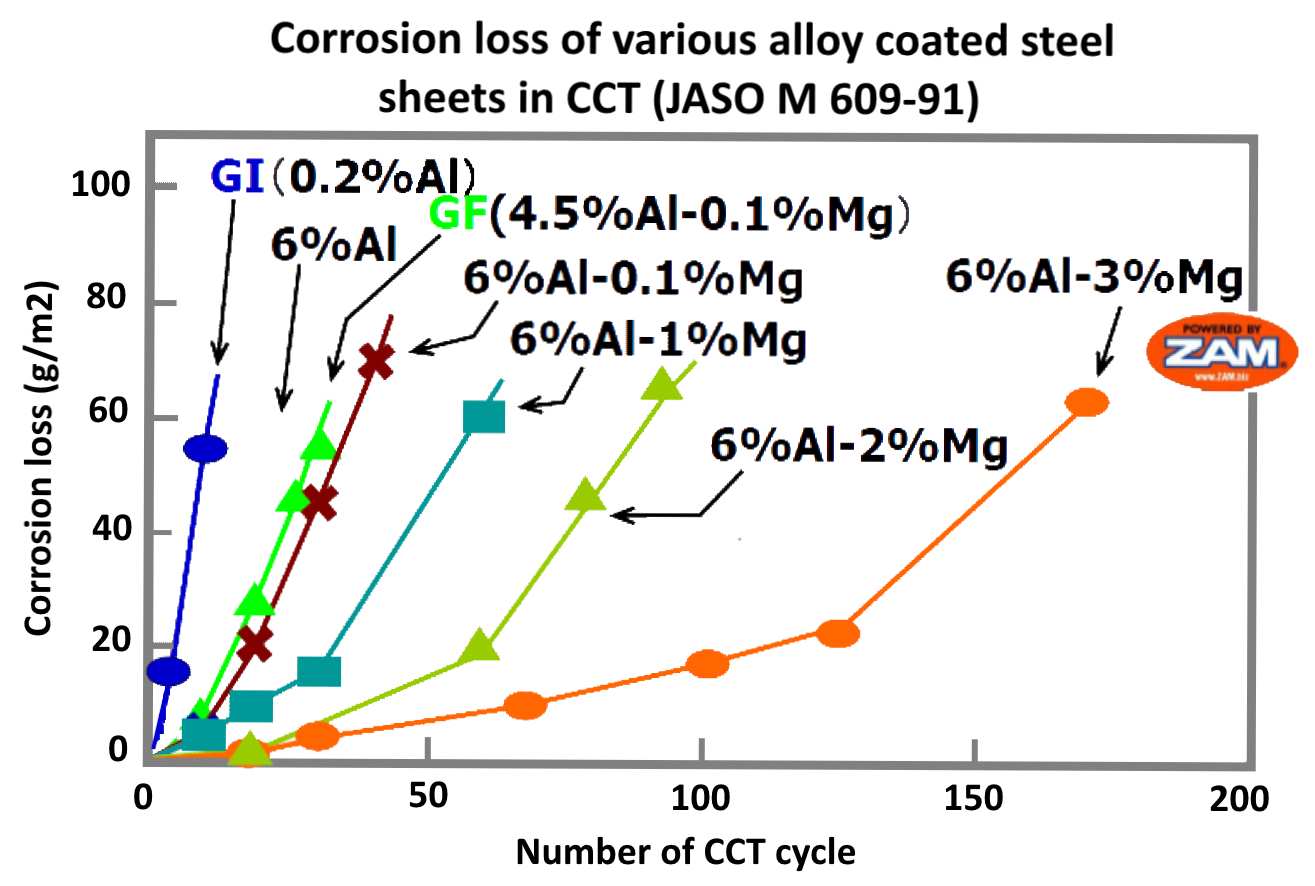
Testing
After thousands of hours of testing and realizing that magnesium greatly enhanced the corrosion resistance of zinc coatings, NIPPON STEEL found the composition of elemental metals to best enhance the corrosion protection of sheet steel. The highest corrosion resistance was observed at 3% Mg, with a significant difference in performance between 2% Mg and 3% Mg.
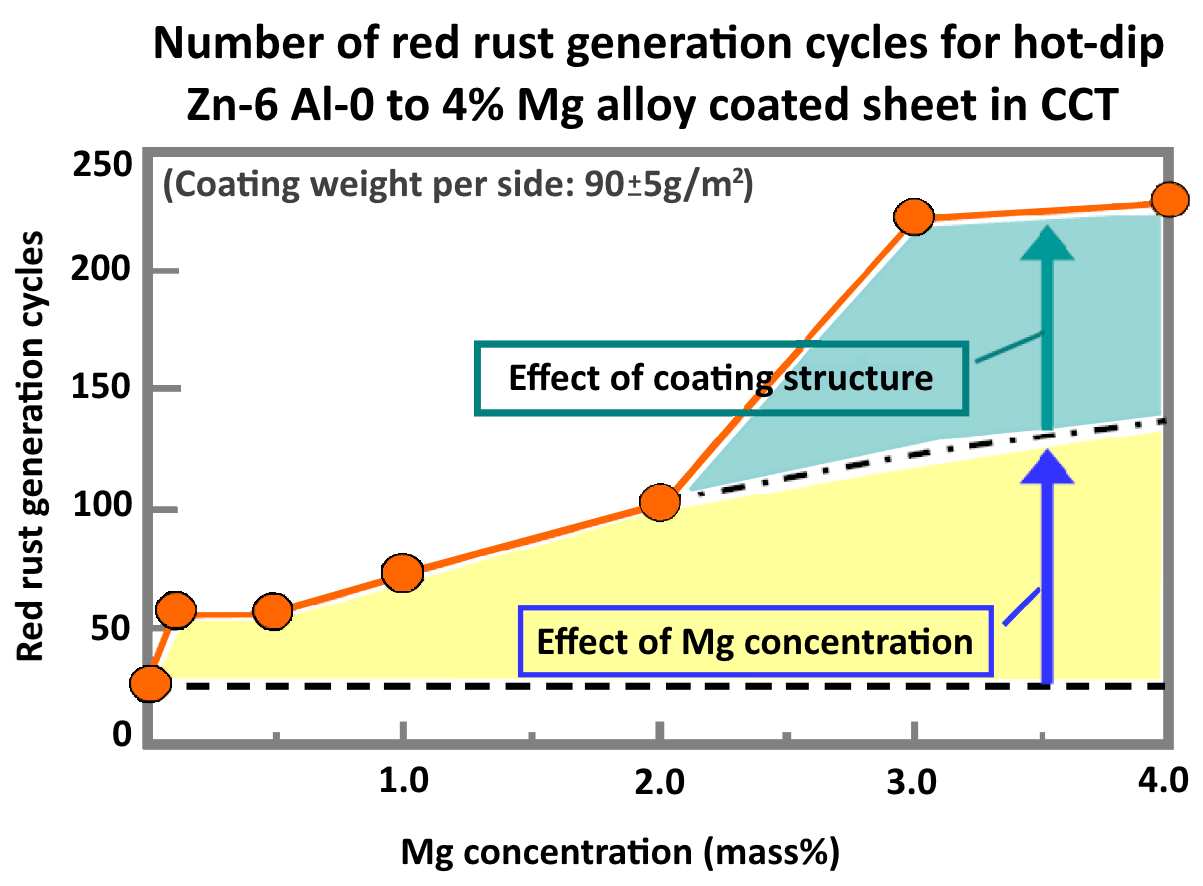
ZAM®'s Unique Coating
The corrosion products formed on ZAM® mainly consist of zinc chlorides and carbonates. The corrosion products formed on ZAM®, unlike galvanized, are almost devoid of zinc oxides. Zinc oxides are large in structure and do not allow for a tightly adhering corrosion layer unlike the fine and tightly bonding chlorides and carbonates of ZAM®. Zinc oxides, being semiconductors, increase the anodic reaction of the coating, thus increasing the corrosion rate. The lack of zinc oxides in ZAM®'s corrosion products greatly facilitates its corrosion resistance.
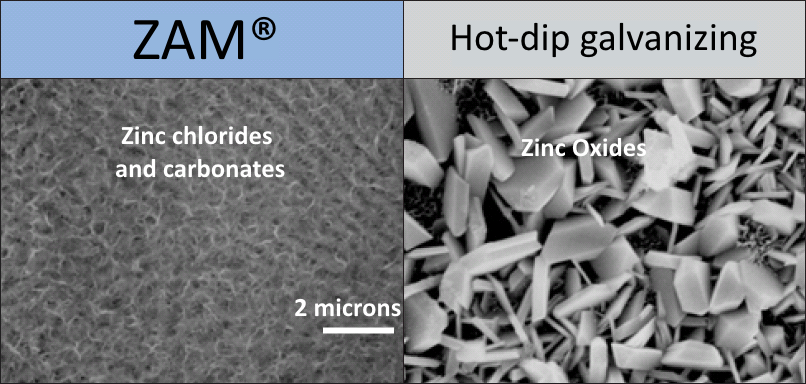
This unique coating develops thin film corrosion byproducts that are remarkably corrosion resistant - even over cut edges. The same corrosion product film that forms on the surface of ZAM® also protects any exposed edge. Over time, this film flows over cut edges with the aid of moisture. This effect is dependent on how wet the environment is, so the more humid an environment the sooner the cut edge will be protected by this film. It should be noted that, since ZAM® is 91% zinc, the cut edges would be protected in the interim by galvanic reaction, where the zinc will sacrifice itself prior to the base steel rusting.